Project overview
A 90km section of a highway contract contains multiple tunnels along the way, and now using one of the arches as an example, a brief analysis of the detailed use of the Rapid Impact Compaction in the construction process of the backfill earthwork is made.
Engineering construction testing and specification.
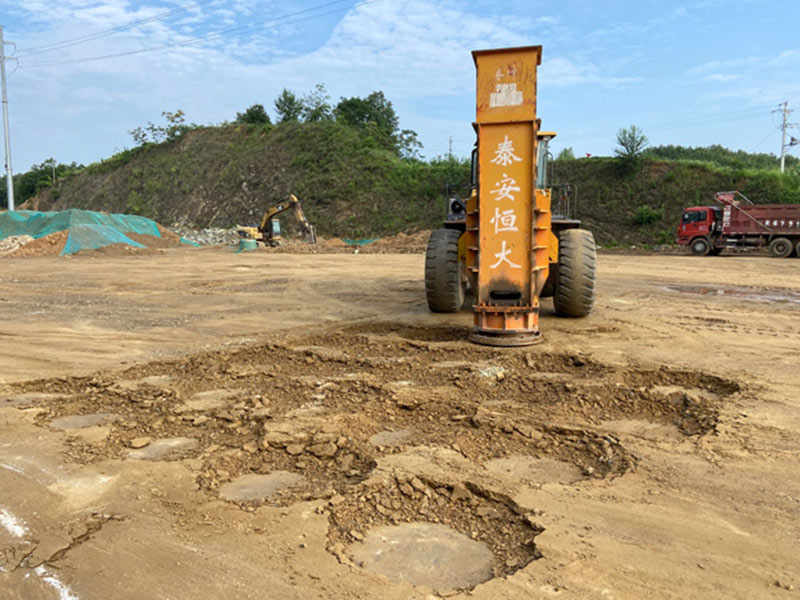
1.Method
(1) First test the design elevation of the backfill soil before the ramming of the Rapid Impact Compaction, and then test the design elevation after 3 ramming and 6 ramming, and finally after a clear foundation settlement transformation.
(2) Compaction of the substrate is solved, and when the sedimentation amount of the interval 2 rammings is changed within 10mm, the compaction within the range of 1m below the pavement is tested on the spot.
2.Specification
The above methods are selected to carry out testing, and when the compaction evaluation conclusion of the Rapid Impact Compaction is 1%-3% greater than the index value, it is regarded as the compaction standard. General provisions for all ramming points are tested, if the ramming point test conclusion does not achieve the above provisions, it is necessary to immediately carry out ramming, to meet the requirements.
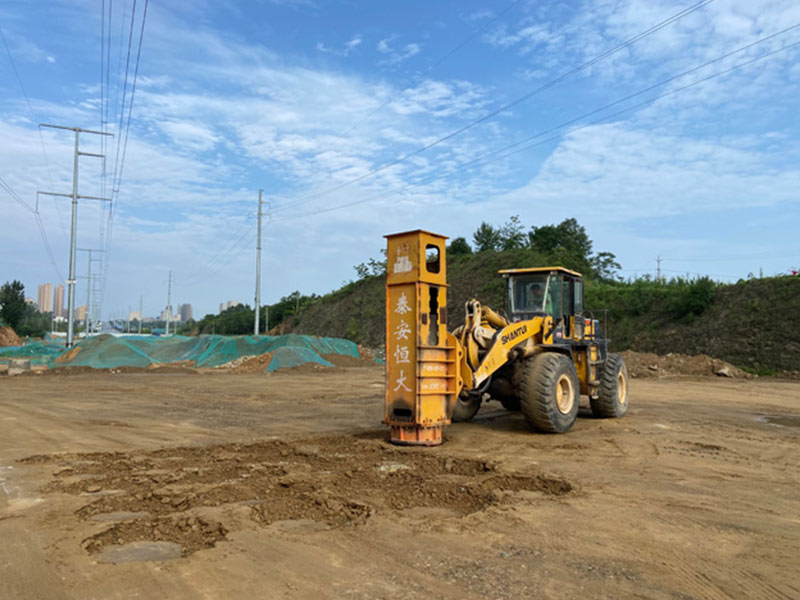
Detection conclusions and profiling
The main parameters of the construction of this building are selected as follows: the four-stroke ramming hammer of the Rapid Impact Compaction is manipulated according to 120cm, and the ramming is carried out in 2 times, and the ramming force is selected at the high end of each ramming.
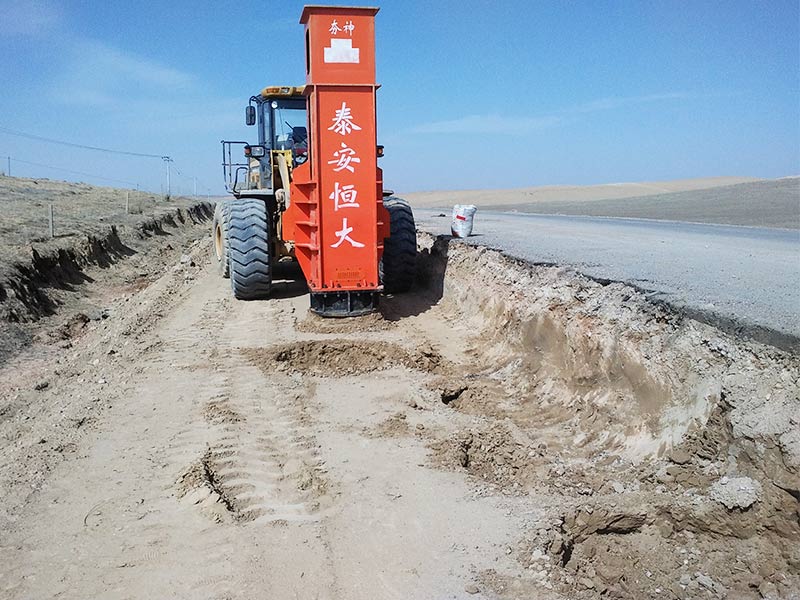
Strictly implement the method verified and approved by the engineer to achieve engineering construction, and detect the settlement transformation of the foundation after the operation, the conclusion is: (1) the four ramming points with a layer thickness of 80cm, the average elevation difference is 4.0cm, the maximum value is 4.2cm, the minimum value is 3.9cm, and the distance is not significant; (2) the four ramming points with a layer thickness of 120cm have an average elevation difference of 4.6cm, the maximum value is 4.7cm, the minimum value is 4.5cm, and the distance is not significant; (3) the four ramming points with a layer thickness of 160cm. The average elevation difference is 5.1cm, the highest value is 5.2cm, and the minimum value is 5.0cm, and the distance is not significant; (4) the average elevation difference of the four ramming points with a layer thickness of 200cm is 5.6cm, the highest value is 5.7cm, and the minimum value is 5.5cm, and the distance is not significant.
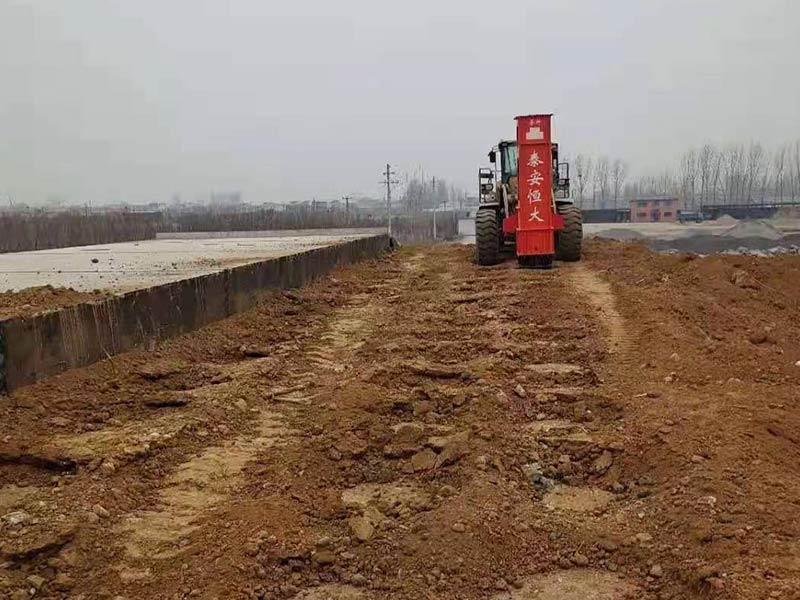
The compactness test results of the Rapid Impact Compaction are as follows: (1) the compactness of three compaction points with a layer thickness of 80cm is increased by 2.9%, 2.3% and 2.3% respectively after compaction; (2) For the three compaction points with a layer thickness of 120cm, the compactness will be increased by 2.0%, 2.0% and 2.1% respectively after compaction; (3) For the three compaction points with a layer thickness of 160cm, the compactness will be increased by 1.9%, 2.0% and 2.0% respectively after compaction; (4) For the three compaction points with a layer thickness of 200cm, the compactness will be increased by 2.1%, 2.0% and 2.2% respectively after compaction.
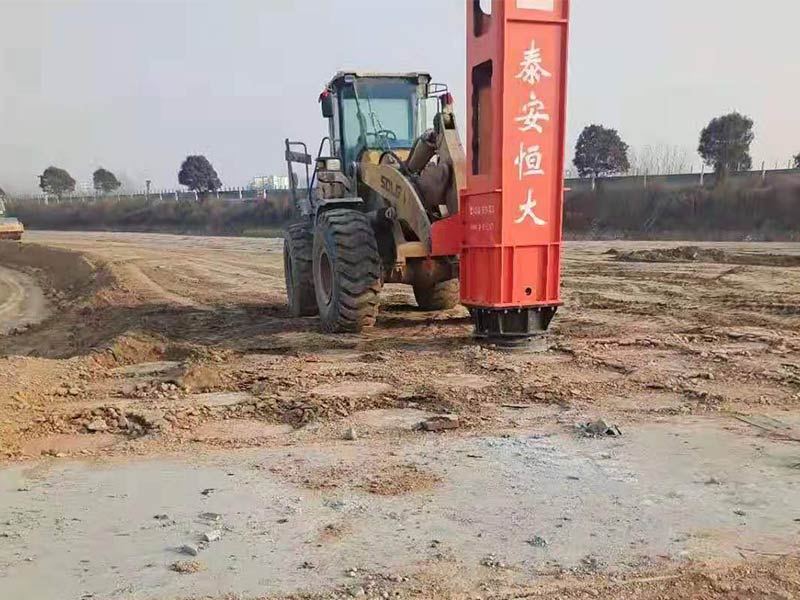
From the above test conclusions, it can be seen that the back of the roadbed has been reasonably ribbed, and according to the effective use of the Rapid Impact Compaction, it can further improve the compaction, promote the settlement of the natural foundation, ensure the overall quality, reduce or prevent the occurrence of problems such as bridge head jumping from the source. From the Rapid Impact Compaction compaction detection conclusion, it is known that the difference in the amount of compaction increase of different layer thickness rammer points is not large, according to the rationality of the equipment and the high efficiency of work, the best ribbed layer thickness can be clearly defined as 160cm, that is, every backfill 160cm to carry out a ramming rib.