RIC is a technique allied to Dynamic Compaction that can be used to increase the bearing capacity of soils through controlled Impact. The treatment is effective in the top layers of soil, typically up to 6m depth, though improvements up to a depth of 9m have been seen in some conditions.
Drop weights of 10 tonnes are used on our HC150 machines respectively and are dropped from heights of 1.2m – 1.5m onto a special foot assembly at 40 – 90 times per minute. The foot remains in contact with the ground at all times.

The Rapid Impact Compaction for the soil improvement uses a hydraulic hammer mounted on an excavator. The hammer with a weight ranging from 5 up to 12 tons is dropped freely from a height of 1.2 m on a large circular foot. Impacts repeated at a rate ranging from 40 up to 60 blows per minute plunge the steel foot creating a crater.
The control system installed in the operator’s cab allows for controlling the compaction process and recording the parameters such as impact energy or foot penetration. It can also be used to change the height from which the hammer is dropped.
The compaction in the RIC technology is usually preceded by creating a test plot where the compaction is performed for various spacing and rates of blows. Then, the local compaction of the improved soil is tested and the optimal grid spacing and the number of blows per one point is determined. Depending on the soils, the number of blows varies between 10 and 40 per one point.
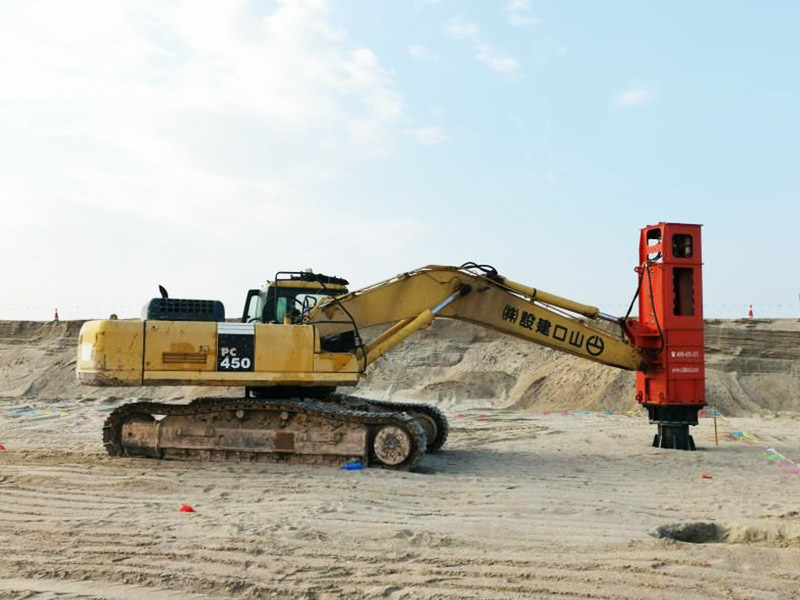
The Rapid Impact Compaction technology works very well for all kinds of non-cohesive soils, especially for the compaction of gravels and sands. It can also be used on reclaimed areas where anthropogenic soils and uncompacted fills occur.
Most often, the RIC technology is used for the construction of enclosed buildings: under the foundation slabs/floors of industrial and commercial halls and under heavy surfaces of warehouses, tanks; for the construction of infrastructure: all types of roads and highways, under the road and rail embankments and often as the improvement of the base for parking lots and airport runways. A great advantage of the RIC method is its mobility and relatively small size of the equipment unit which allows for carrying out the works in areas with difficult access.
Depending on the soil type, water conditions and parameters of the hammer the soil compaction range reaches a depth between 4.0 and 5.0 m.
A safe working distance from the existing buildings, for which vibration monitoring is not necessary, amounts to approximately 5.0 up to 6.0 m. Than, the generated noise is within 90 dBA.
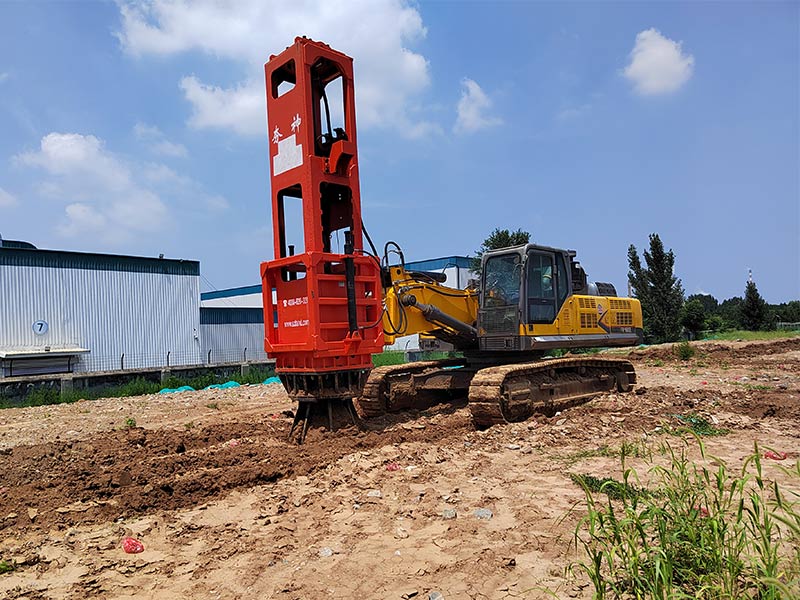
The way in which RIC improves the ground is a “top-down” process, compared to Dynamic Compaction (DC) which is a “bottom-up” process. The first few blows in rapid impact compaction create a dense plug of soil immediately beneath the compaction foot. Further blows advance this plug deeper, which compacts soil in a deeper layer. This process progresses until little further penetration of the compaction foot can be achieved with increasing blows.
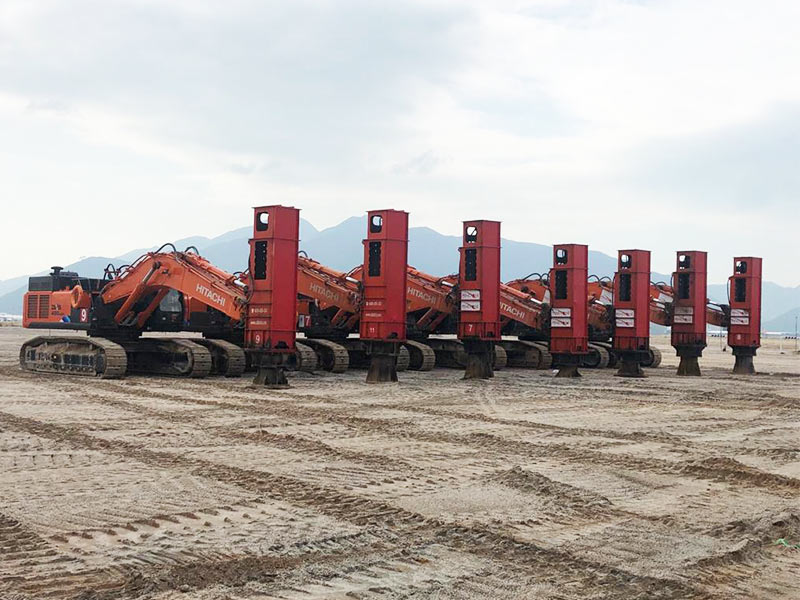
The rapid impact compactor as a means of quickly repairing damage runways. It works by imparting dynamic energy through a falling 'drop-weight, which is dropped from a controlled height onto a patented foot.
With heights of 9 to 12 tones applied to the foot , the 'drop-weights' falls from relatively short height of only 1.2 meters at a rate of 40 to 60 times a minute.
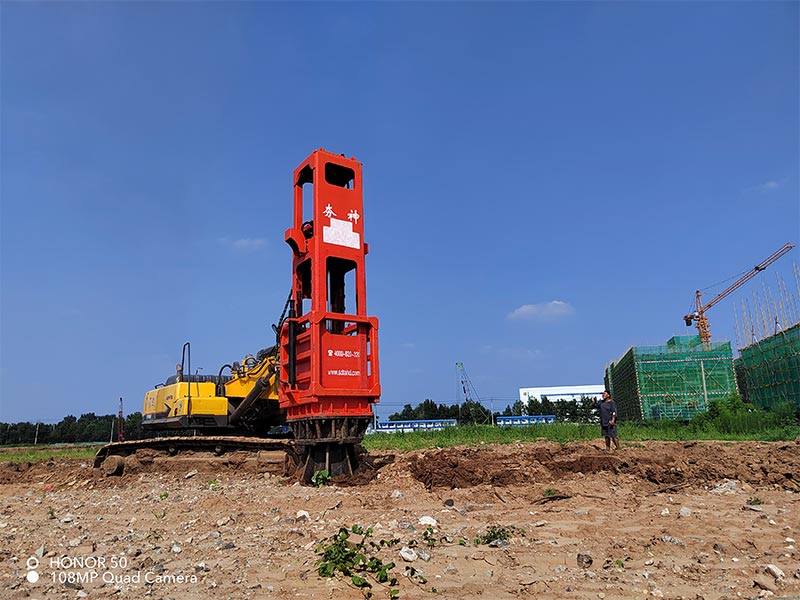
Effective compaction depths vary with the nature of hte soil compacted, but depth of up to 8m have been reached with a 9t rig.
This results in The Rapid Impact Compactor transferring energy to the ground in a significantly more effective manner as the 'foot' stays in contact with the surface, never actually leaving the ground. It is because of this impacting sequence that we can ensure that the transfer of energy into the ground is carried out in the most efficient way possible.