The dynamic compaction technology used in Rapid Impact Compaction fills the gap between traditional surface compaction technologies such as rolling and vibratory compaction and traditional strong compaction techniques. According to the research and test results, the compaction depth of the Rapid Impact Compaction is 1-4m, and the impact depth is 4-10m, second only to strong compaction, which is greater than various compaction machinery, including iThe trial was divided into two trials. The first is the density chasing test of Rapid Impact Compaction after subgrade filling and compaction. The purpose of the test is twofold: One is to measure the increase and settlement of compaction after Rapid Impact Compaction; The second is to measure the number of impacts required to achieve the appropriate level of compaction and sedimentation.
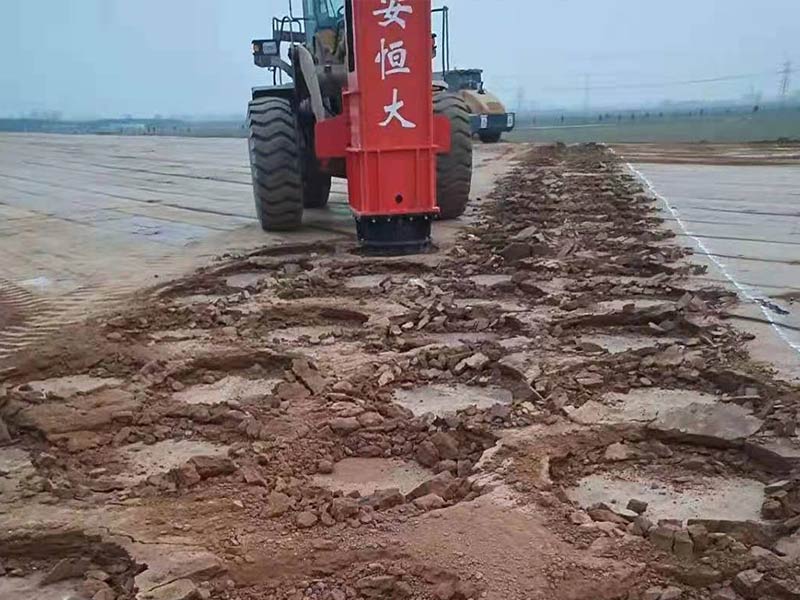
The second is to determine the general subgrade compaction test. The purpose of the test is twofold: first, the loose thickness and sedimentation when the compaction meets the design requirements; The second is to determine the corresponding number of impacts after meeting the requirements.
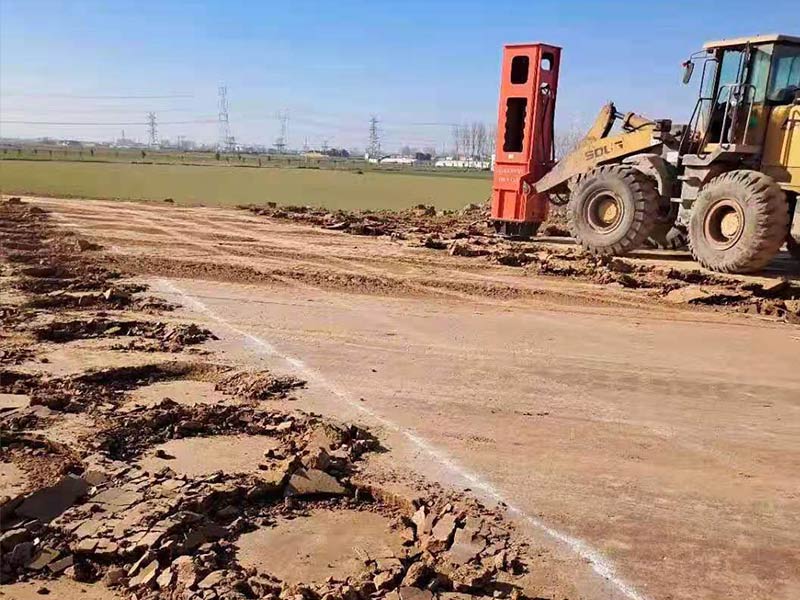
Test 1
(1) Construction preparation.
Select the test section on the K46+700 subgrade. After the compaction degree is qualified, the test section with a width of 10 m and a length of 25 m is sprinkled with lime wire for the compaction test.
(2) Ramming point arrangement.
Use gray lines to draw a test range of 21.5m × 5.75m wide. According to the diameter of the rammed plate of 90cm and the range of the Rapid Impact Compaction, the center spacing of the rammed plate for the two tampons is set to 1.4m. The center of each ramming point is marked with lime.mpact rollers.
(3) Tamping.
Rapid Impact Compaction should be compacted according to the position of the compaction point arranged. When compacting, compaction should be carried out according to the strong compaction parameters determined by testing and design. A person directs the landing site before the Rapid Impact Compaction to ensure the accuracy of the compaction position. The compaction sequence is compacted from the edge to the center.
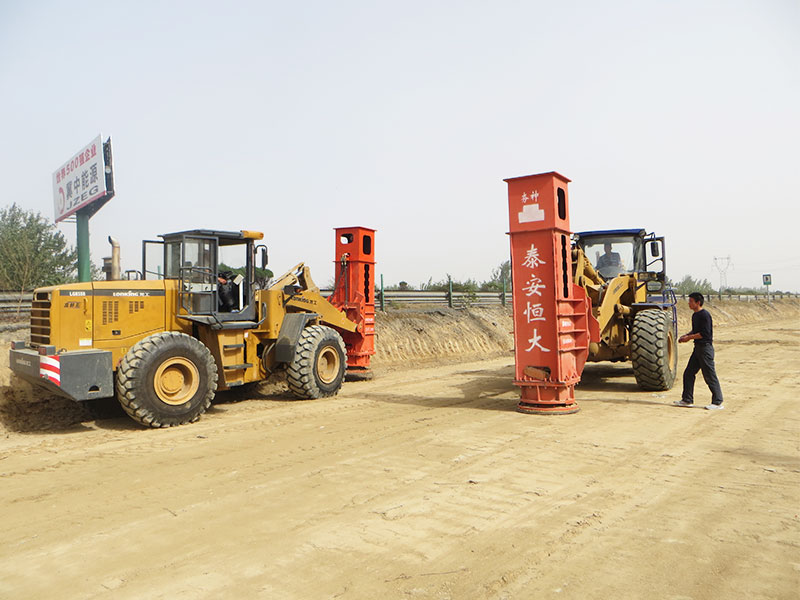
Test 2
(1) construction preparation.
Select the test section on the K46+700 subgrade. Pile the soil with a nearly optimal moisture content after drying on the subgrade. The mound is 25m long, 15m wide and 1m high to leave enough room for Rapid Impact Compaction. Draw the construction drawings, indicate the ramming point number, and the site is lofted according to the design scope, and reported to the supervision engineer for acceptance.
Backfilling should control the moisture content and then be within the optimal moisture content range. If the moisture content is lower than the optimal moisture content, drilling irrigation or sprinkler immersion can be performed. The backfill surface is bulldozed with a bulldozer and scraped flat with a vibratory roller, without obvious settlement, ensuring safe and uniform construction of the compactor.
(2) Ramming point arrangement.
As with the chasing test, a 21.5×5.75 m wide test range is drawn with a gray line, divided into three sub-segments, each of which is 6.5 m long and 5.75 m wide. The first paragraph rammers 3 times for each ramming point, the second paragraph rammers 6 times for each ramming point, and the second paragraph rammers 9 times for each rammed point.
(3) Tamping.
Rapid Impact Compaction should be compacted according to the position of the compaction point arranged. When compacting, compaction should be carried out according to the strong compaction parameters determined by testing and design. A person directs the landing site before the Rapid Impact Compaction to ensure the accuracy of the compaction position. The compaction sequence is compacted from the edge to the center.
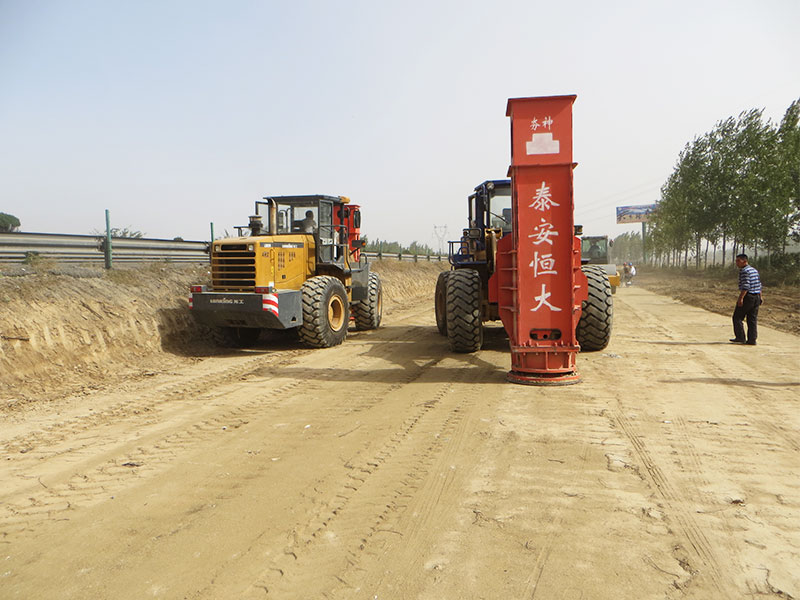
From the above test data, it can be seen that the number of times test 1: chasing and compacting is 6 times. After the compaction, the average compaction can be increased by 4.2%, and the average settlement is 7.9cm; test 2: the general filling compaction is less than 80cm, and the compaction degree meets the requirements of the general subgrade filling compaction degree is 9 times, and the average settlement is 26.2cm; therefore, the general filling loose paving can be controlled at 80~100cm layer.
According to the structural characteristics of Rapid Impact Compactions, the working surface required for hydraulic compaction is relatively small, which meets the construction requirements of the backfill of the standard section and the back backfill of the gravity retaining wall. Working where large rollers cannot work has obvious advantages, which can not only ensure the quality of construction, but also speed up the progress of the project.