The control system installed in the operator’s cab allows for controlling the compaction process and recording the parameters such as impact energy or foot penetration. It can also be used to change the height from which the hammer is dropped.
The compaction in the RIC technology is usually preceded by creating a test plot where the compaction is performed for various spacing and rates of blows. Then, the local compaction of the improved soil is tested and the optimal grid spacing and the number of blows per one point is determined. Depending on the soils, the number of blows varies between 10 and 40 per one point.
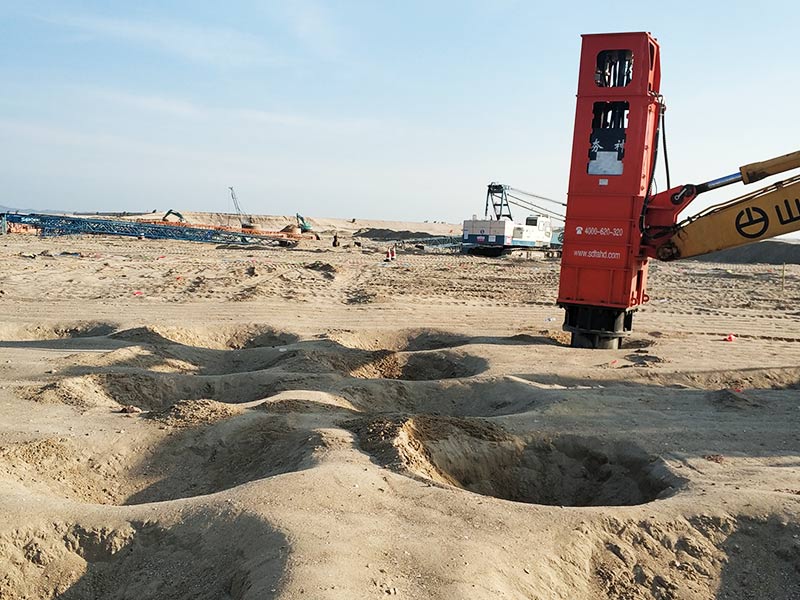
The Rapid Impact Compaction technology works very well for all kinds of non-cohesive soils, especially for the compaction of gravels and sands. It can also be used on reclaimed areas where anthropogenic soils and uncompacted fills occur.
Most often, the RIC technology is used for the construction of enclosed buildings: under the foundation slabs/floors of industrial and commercial halls and under heavy surfaces of warehouses, tanks; for the construction of infrastructure: all types of roads and highways, under the road and rail embankments and often as the improvement of the base for parking lots and airport runways. A great advantage of the RIC method is its mobility and relatively small size of the equipment unit which allows for carrying out the works in areas with difficult access.
Depending on the soil type, water conditions and parameters of the hammer the soil compaction range reaches a depth between 4.0 and 5.0 m.
A safe working distance from the existing buildings, for which vibration monitoring is not necessary, amounts to approximately 5.0 up to 6.0 m. Than, the generated noise is within 90 dBA.
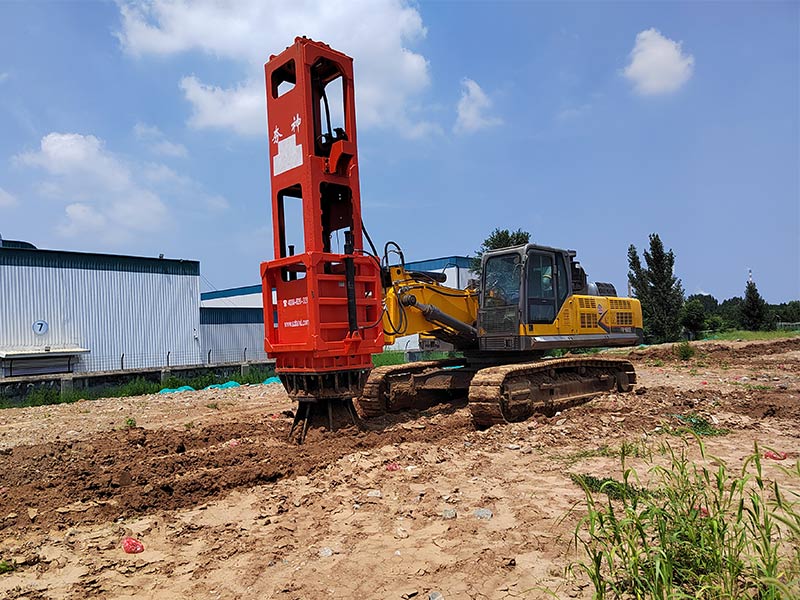
During the compaction of a location, the foot remains into contact with the soil. The impact of the hammer on to the foot initiates the compaction process. The movement of the foot into the ground, the heavy weight of the equipment and high energy transfer is also causing densification. The dense compaction grid ensures that a homogeneous compaction is reached throughout the area. This is caused because the impact locations are also affected by the compaction of nearby points which results in improving the overall performance.
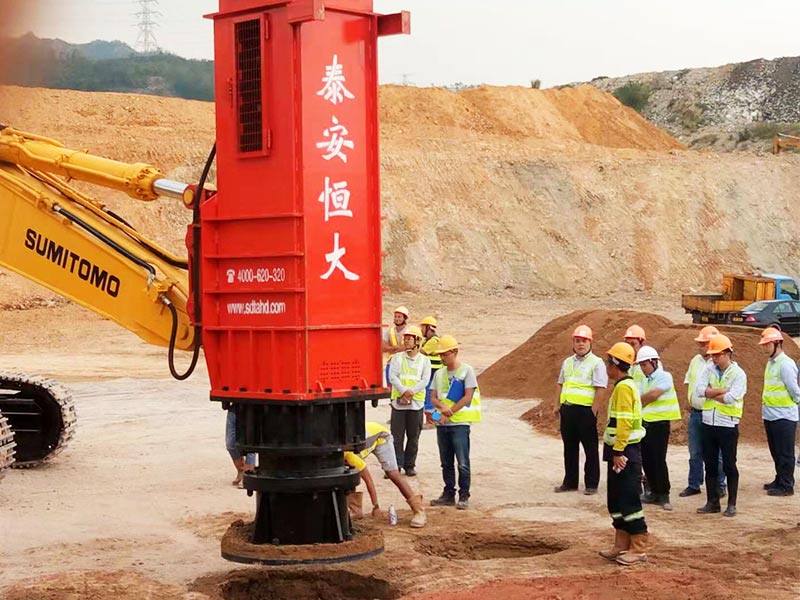
The way in which RIC improves the ground is a “top-down” process, compared to Dynamic Compaction (DC) which is a “bottom-up” process. The first few blows in rapid impact compaction create a dense plug of soil immediately beneath the compaction foot. Further blows advance this plug deeper, which compacts soil in a deeper layer. This process progresses until little further penetration of the compaction foot can be achieved with increasing blows.
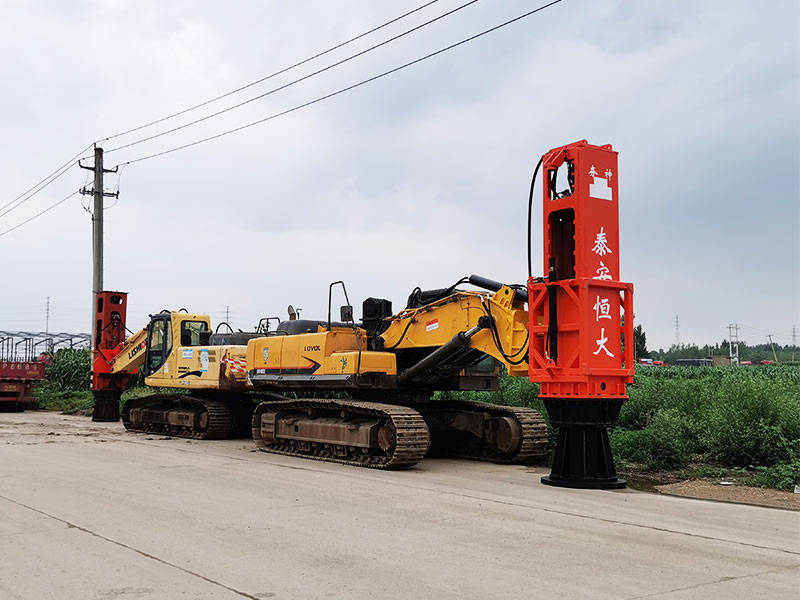
This compaction energy brings the soil particles into a more densely packed structure. The compaction energy is transmitted safely and efficiently as the compaction foot remains in contact with the ground. No flying debris occurs during the compaction process. The hammering of the foot by the impact weight is the reason of the sub-soil compaction. Indeed, the huge amount of energy developed upon the hammering process and transmitted to the ground through the foot, pushes the backfilling material into a denser structure.