Tamping rammers are better for clay soils and smaller areas. They compact the soil through impact. Plate compactors are best for gravel, sand or silt and larger areas and compact through vibration. Consider your soil type and size of the job when choosing a tamping rammer vs plate compacter.
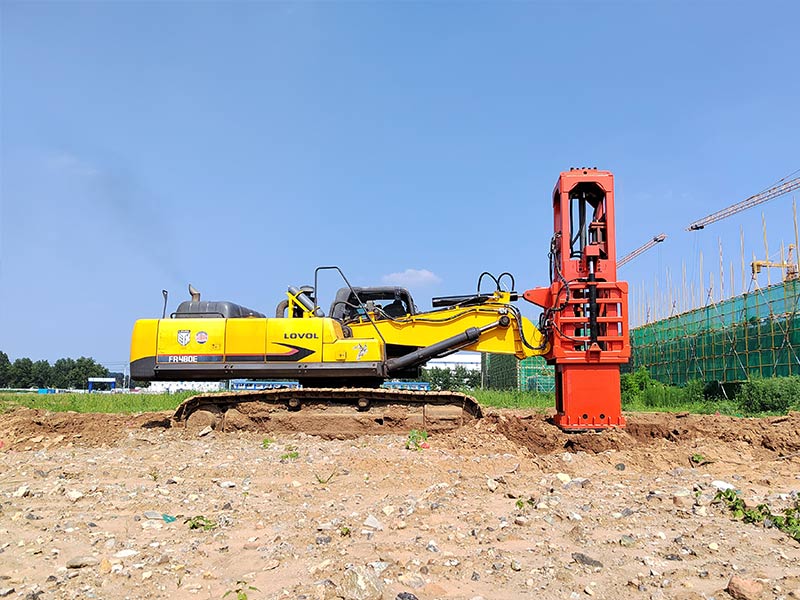
A compaction plate is placed on the ground to be treated. A hydraulic hammer, generally weighing less than 10 to 15 tonnes, is fitted to an excavator and used to transmit compaction energy to the soil via repeated impact. Without specific site precautions, a safe working distance to sensitive structures can usually be defined on the order of 8 to 10 m, as a distance of 5 to 6 m can usually be adopted for classical structures. At that distance, noise levels are lower than 90 dBA.
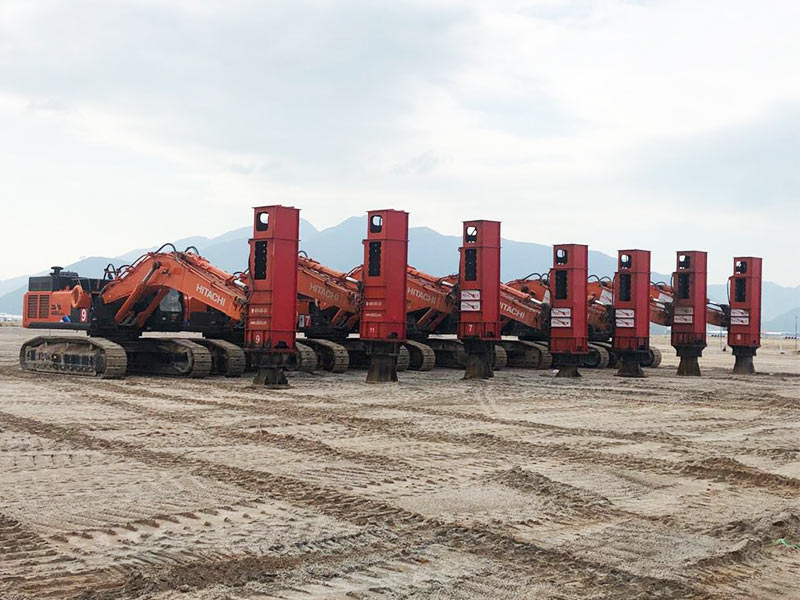
It is possible to compact the ground near an adjacent site with rapid impact compaction. Rapid impact compaction suits to ground improvement in small spaces. As an example, we can apply this technique within or next to existing warehouses. In such cases, we monitor very carefully vibrations in adjacent structures during rapid impact compaction.
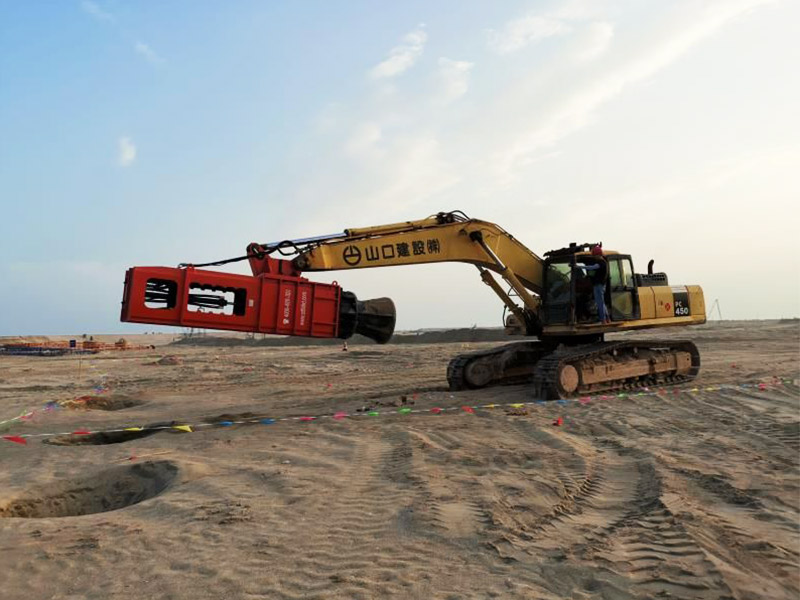
The RIC technology is the modern approach for compacting existing soils that would otherwise be excavated and compacted using a conventional roller compactor in layers of 15 to 30cm.
Energy is transferred to the underlying loose granular soils rearranging the particles into a denser formation. RIC can effectively densify up to 4-5m of soils without excavation, adding water or dewatering. It can also be used for fill compaction, which can place in bulk fill materials and compact it accordingly without adding any water.
For large infrastructure developments, RIC takes the lead due to its speed of execution that makes it much more cost effective than other alternatives.
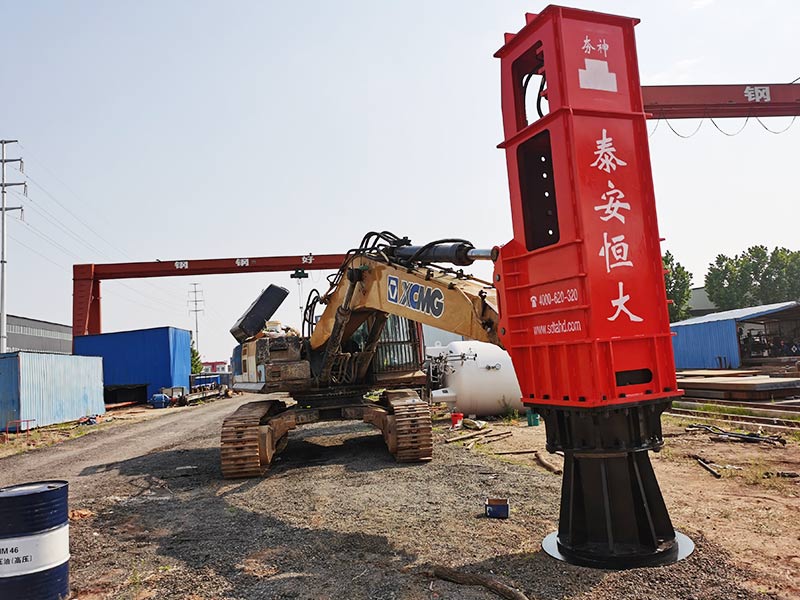
The energy and deflection of the soil is monitored and recorded at each location, which allows the geotechnical engineer to determine when effective treatment is complete. It also enables the engineer to identify weak zones (red dots) or debris zones throughout the pad so that any remedial actions that may be required can be minimized resulting in cost savings.
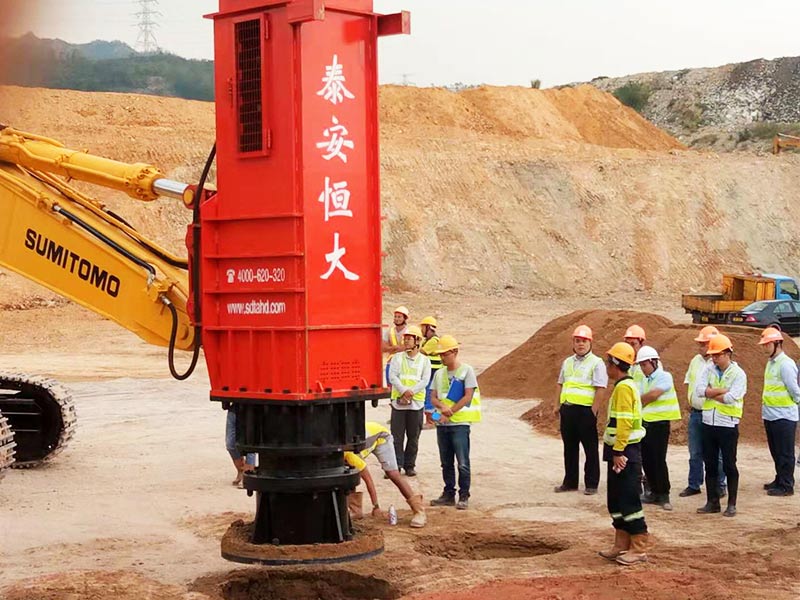
The Rapid Impact Compaction for the soil improvement uses a hydraulic hammer mounted on an excavator. The hammer with a weight ranging from 5 up to 12 tons is dropped freely from a height of 1.2 m on a large circular foot. Impacts repeated at a rate ranging from 40 up to 60 blows per minute plunge the steel foot creating a crater.
The control system installed in the operator’s cab allows for controlling the compaction process and recording the parameters such as impact energy or foot penetration. It can also be used to change the height from which the hammer is dropped.
The compaction in the RIC technology is usually preceded by creating a test plot where the compaction is performed for various spacing and rates of blows. Then, the local compaction of the improved soil is tested and the optimal grid spacing and the number of blows per one point is determined. Depending on the soils, the number of blows varies between 10 and 40 per one point.