Rapid Impact Compaction equipment also known as "hydraulic compactor", "impact compactor", "hydraulic impact compactor", is a compaction machine that uses the combined force of machine gravity and variable force to compress soil, including excavator Rapid Impact Compaction equipment and loader Rapid Impact Compaction equipment.
Due to the lack of construction experience, users who first use the Rapid Impact Compaction equipment often have such questions: how many hammers does the hydraulic impact compactor tamp? How thick is the one-time compaction?
The Rapid Impact Compaction equipment is divided into large and small models. At the same time, it is divided into three working gears: strong, medium and weak. In addition, there is no "standardized" regulation on how many hammers to tamp at a time, due to the differences in the soil properties of the subgrade. The number of hammers to be tamped by the hydraulic tamper needs to be tested and tamped to finally determine.
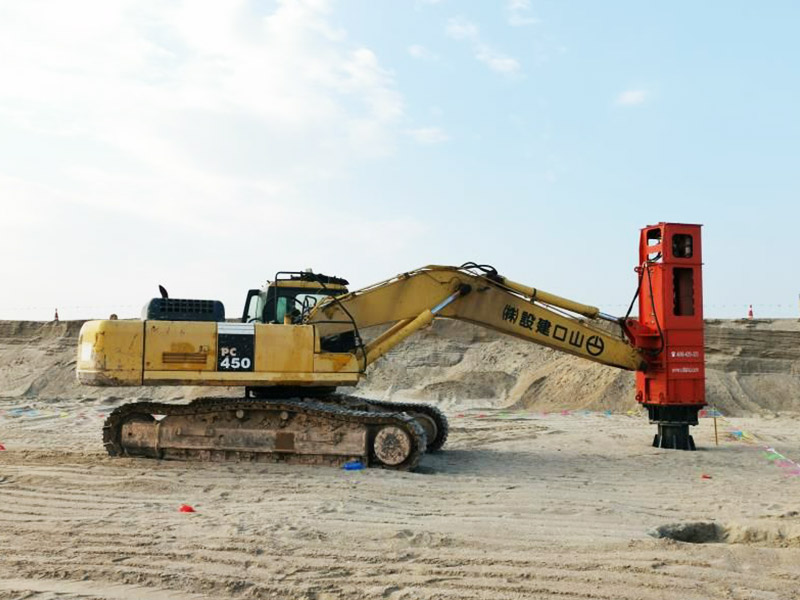
The test compaction of Rapid Impact Compaction equipment is usually carried out at the actual construction site, specifically: 1-step 9-hammer, 12 hammer, 15 hammer point compaction; 2 gears, 6 hammers, 9 hammers and 12 hammers are used for point compaction; 3 gears, 6 hammers, 9 hammers, 12 hammers, point distribution and compaction; Measure the compactness after tamping, and finally tamp according to the standard gear and the corresponding number of hammers.
The test compaction can be carried out according to the following steps:
1. Test preparation: before compaction, the test subgrade section must be inspected according to the compaction standard and flatness required by the design. After passing the inspection, the impact compaction points can be arranged. For the test compacted subgrade section, the site shall be leveled and rolled before impact compaction according to the preparation items before construction. When the surface of the filling layer is dry, an appropriate amount of water should be sprayed to prevent the surface from being dusted, which will affect the transmission of energy to the deep layer.
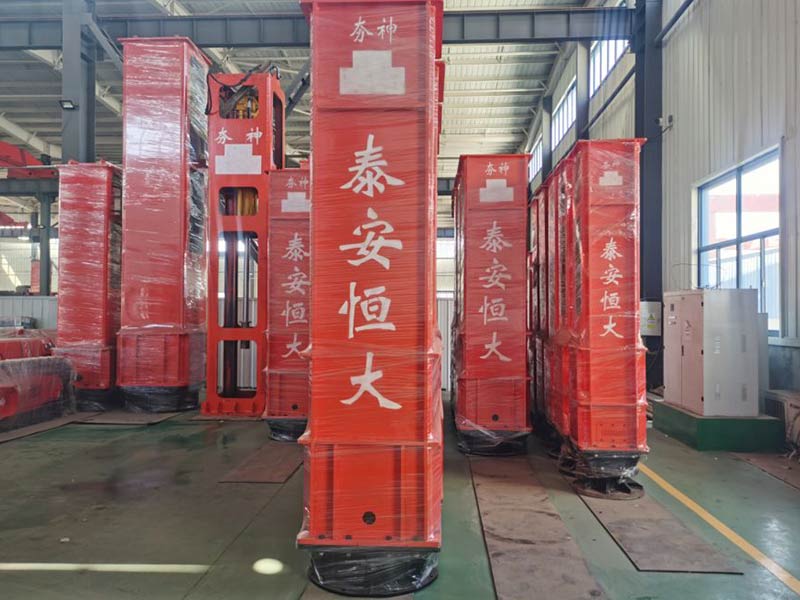
2. Tamping arrangement: set out tamping points on the Subgrade after the construction is completed and tested to be qualified according to the compaction standard required by the design, mark and number them with white ash, and then measure the initial elevation of each point according to the number. The hydraulic tamper shall be in place according to the position of measurement and setting out, so that the tamper is aligned with the point.
3. According to its tamping energy, the Rapid Impact Compaction equipment is divided into three working gears: strong, medium and weak. Adjust the hydraulic impact rammer to their respective gears respectively, record the tamping according to different hammer numbers, measure and record the settlement of the tamping point.
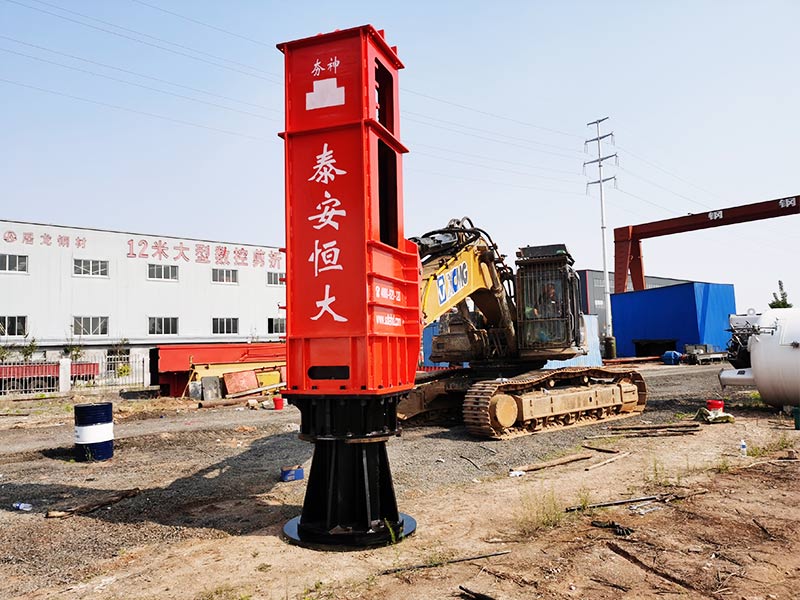
During construction, the construction gear shall be reasonably selected according to the site conditions, such as whether there are culverts and pipelines below, whether there are impact force restrictions on adjacent structures, etc.
4. Take every 3 hammers as a group, accumulate and record the settlement of every 3 hammers.
5. Repeat items 3-4 until the impact compaction of the 6th, 9th and 12th hammers of the corresponding design is completed, and the settlement of each 3 hammers is accumulated and recorded.
Determine the number of working hammers through the test, and refer to the previous site experimental data, and finally determine which gear and the corresponding number of tamping hammers have the best tamping effect. Note that the high vibration frequency of the weak gear can also achieve the ideal effect, not the strong gear, and the tamping effect must be the best.
6. After a single tamping point meets the tamping requirements, move the machine to tamp the next point, usually using the straight-line operation method. The construction position of Rapid Impact Compaction equipment is mostly at the back of bridge and culvert abutment. In order to facilitate the walking of machinery, it is suitable to adopt the straight-line operation method, that is, each single point operation, forward or backward operation to the next point.
7. During the construction of Rapid Impact Compaction equipment, it is suitable to adopt the layout of intermittent operation points: the edge of each tamping point is separated by a certain distance, and the points are arranged in an equilateral triangle, that is, the point distribution method with the spacing of 50cm between the edges of each hammer is adopted.
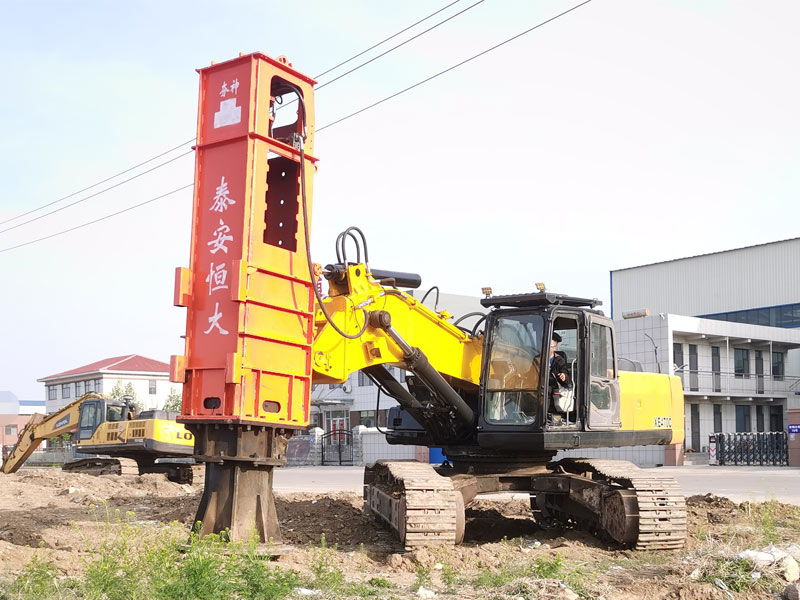
The small distance between the outer edge of the rammer of the operation point of the Rapid Impact Compaction equipment and the bridge and culvert structures shall be determined according to the field test. According to the experimental parameters, it is suggested that the distance between the center of the rammer at the construction point of the row and the structure can be set as 80cm, that is, the distance from the edge of the rammer to the structure is 30cm, which can ensure the safety of the structure.
If the above test methods fail to meet the construction requirements, the number of tamping can be appropriately increased. If a certain number of tamping times still fail to meet the requirements, the construction scheme should be considered to be changed.
How many hammers does the Rapid Impact Compaction equipment tamp at a time? In addition to adopting suitable construction technology, it should also be combined with the characteristics and performance of the hydraulic compactor. At the same time, it should also be determined according to the actual working conditions of soil types during construction and their physical and mechanical properties, as well as the objective and natural environment on site, as well as the highway grade and compaction requirements of the construction. The final decision is to obtain the actual data and results through experimental compaction.