RIC typically employs a 7 tonne weight dropped repeatedly through 1.2 m onto a 1.5 m diameter steel articulated compaction foot. Whilst the energy per blow is not large (typically 8.4t.m), the equipment permits a large number of impacts to be applied at a rate of about 40 blows per minute. The operator monitors and can record the number of impacts, the total energy input applied, the foot penetration per blow and the cumulative penetration. When a specified parameter is reached, for example, foot penetration or set per blow, the equipment is moved to the next treatment/tamping point. As the foot remains in contact with the ground, the energy is applied more efficiently in compacting the ground than in conventional drop weight dynamic compaction where the weight may fall on an irregular surface in such a way that much of the energy is dissipated in deforming the irregularities of the ground.
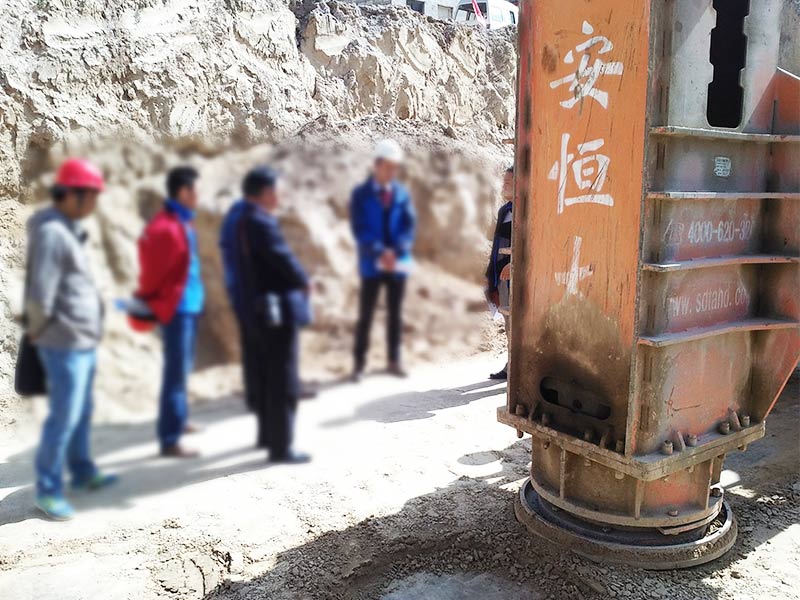
Both field trials and laboratory simulations of RIC have shown that the manner in which the ground responds to treatment is a “top-down” process, compared to DC which is a “bottom-up” process. The first few blows in rapid impact compaction create a dense plug of soil immediately beneath the compaction foot. Further blows advance this plug deeper, which compacts soil in a deeper layer. This process progresses until little further penetration of the compaction foot can be achieved with increasing blows. The effect of the compaction process is confined largely to the ground vertically below the compaction point and treatment is therefore carried out on a closely spaced square or triangular pattern or sequenced on an arc about the centre of rotation of the base machine for the RIC equipment. Additional passes are typically offset from the primary pass to ensure effective treatment coverage. The carrier vehicle is typically a hydraulic excavator.
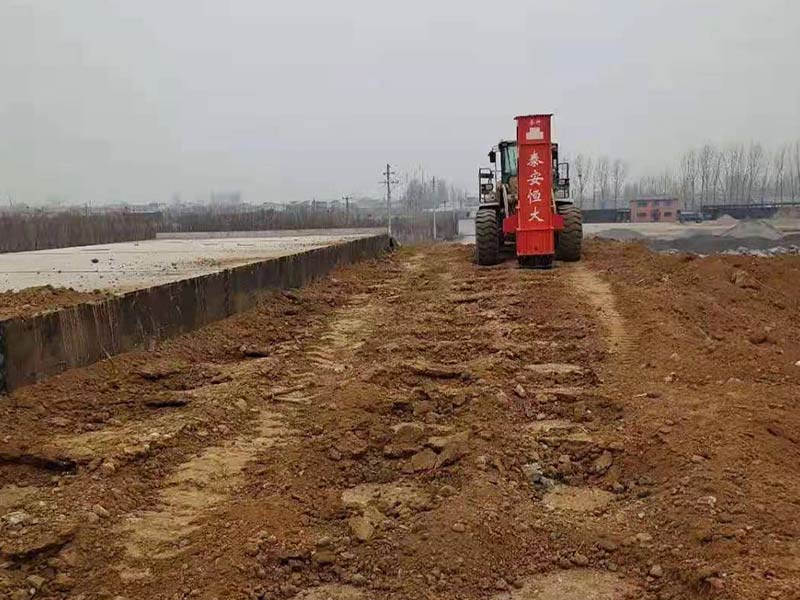
In the urban environment, the RIC technique has a number of specific advantages compared to the conventional drop weight dynamic compaction (DC) technique. These can be summarised as follows:
• The dedicated plant used is relatively small, with moderate mobilisation and operating costs compared with conventional drop weight dynamic compaction. Thus, smaller sites may be economically treated. Rigging and de-rigging times are also quite rapid.
• Treatment can be carried out in closer proximity to existing structures and services vulnerable to vibration damage. There is generally no danger from flying debris.
• Discrete, relatively small foundation areas can be treated without compromising production.
• Energy is more efficiently transferred through the compaction foot which remains in contact with the ground. It is important to recognise that those specifying RIC ground treatment understand the nature of the particular treatment process employed and its potential benefits for the ground conditions being considered.
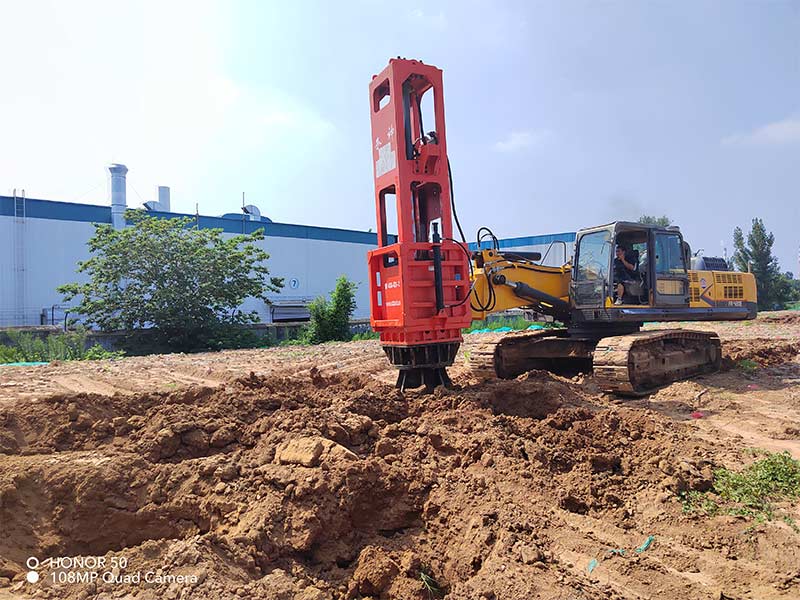
With RIC the total energy input will have a major influence on the depth of compaction. With the rapid impact compactor the energy per blow is very much smaller than conventional DC and the fixed energy per blow of typically 8.4 t.m is not the major influence on the depth of compaction due to the progressive top down improvement of the treated ground. Of much greater significance to the effective depth of compaction is the number of blows at a compaction point or the energy applied overall to the ground surface. For typical impact spacing, 35 blows will impart about 170 tonne.m/m2 of energy. This level of energy input has produced significant compaction to depths between 3 and 4 m in non-engineered generally granular fill and up to about 3 m in natural sand and silty soils using a 7 t hammer.
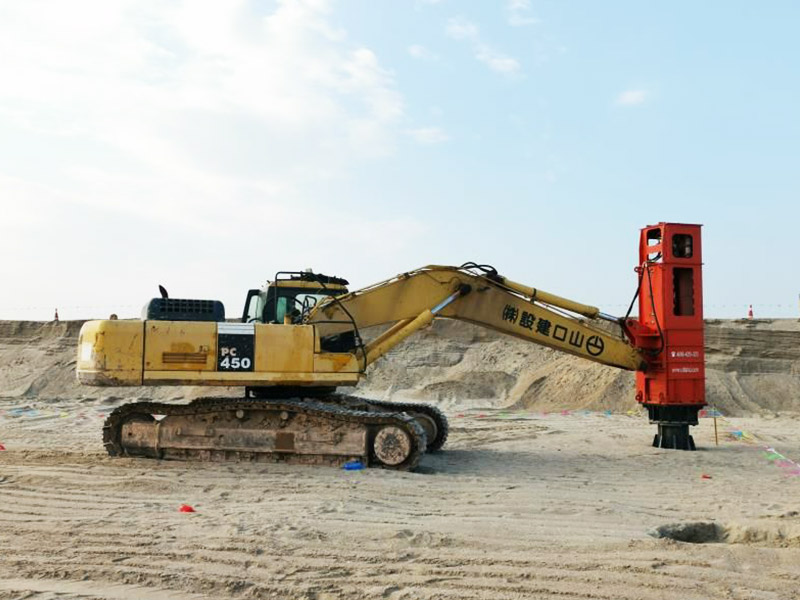
Typical areas of application could include projects such as low-rise structures like housing and schools, embankments, roads and pavement areas. Having the Rapid Impact Compactor mounted on a tracked machine gives it the versatility to move about in narrow and limited height spaces, such as within existing warehouses. With regard to its mobility, the RIC is able to be transported as a single unit, with the impact foot removed and the front end lowered horizontally on a flat-bed trailer. The machine can be ready to work just a few minutes after off-loading. If road restrictions apply, the unit can be easily split into two loads with the excavator travelling separately from the hammer. Re-assembly is achieved in less than two hours.